Test production of blade section finished
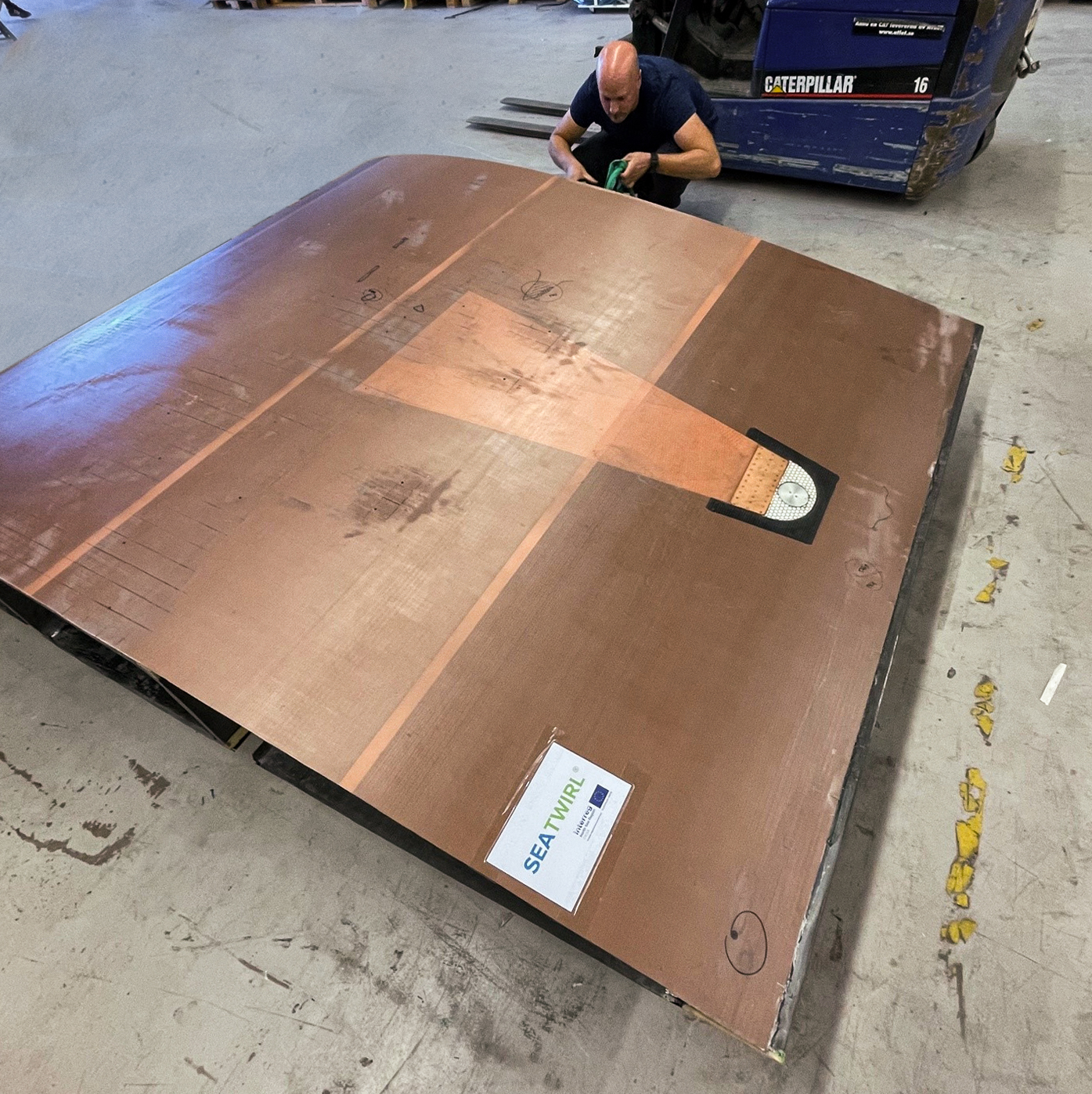
At Elitkomposit in Uddevalla, the test run for the production of blades for SeaTwirl S2x have just finished and been evaluated. As a customer, SeaTwirl follows the process closely to ensure the quality of the finished 40-meter blades.
“We made a two-metre-long test section in the real mould to practice the process. To make 40-metre blades in a relatively thick carbon fibre laminate is not without difficulty. There can easily appear air pockets and such things. So, for us the test run is a way to minimize the risk in the process,” says Martin Rosander, head of blades and struts at SeaTwirl.
With lessons learned from the test, production of the real blades will begin during the fall. The blades will be manufactured in two parts which are then bonded together. With one mould, the process will be repeated six times for three blades.
Since carbon fibre is vulnerable to lightning strikes, the blades are covered in a copper mesh that will conduct the current.
“It is the same technology the aerospace industry uses. Since carbon fibre do conduct electricity, but not very well, it tends to get damaged if lightning strikes. Therefore, we need to protect it with a layer of perforated copper,” says Martin Rosander.
The 25-meter struts are being manufactured at Aston Harald in Hönö with the same process. First a test run where lessons are learned and implemented in the real production.
“Moulds for the struts have been ordered and are on their way to Hönö. The plan is to start laying laminate in the fall,” says Martin Rosander.